
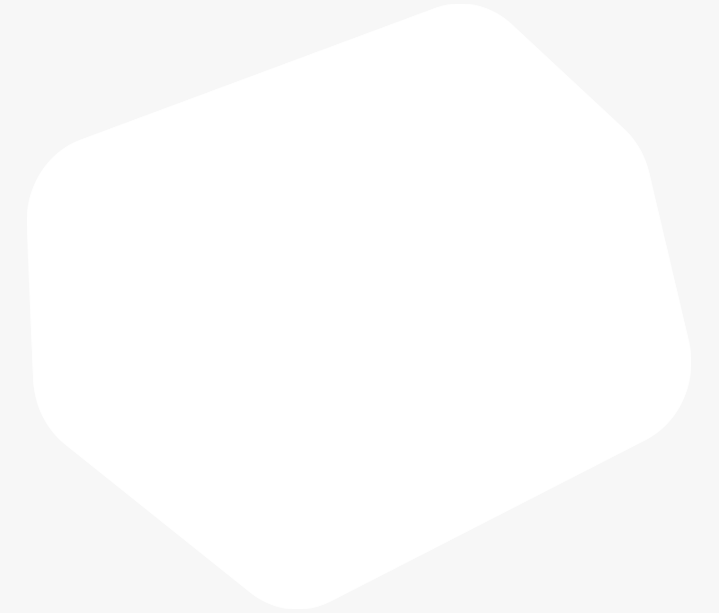
Kruitbosch Halves its Error Rate, Speeds Up Orders and Increases Productivity by 30% with Honeywell’s Vocollect Voice Solutions
Leading Dutch and Belgian bicycle manufacturer and spare parts supplier reduces number of steps in picking and dispatch preparation from four to two, and can now pick more than five times as many concurrent orders
The pressure on suppliers for fast and accurate customer service is constantly increasing. An order placed today means delivery for tomorrow. Such delivery terms can have major consequences for suppliers. This was indeed the case for Kruitbosch, a leading bicycle supplier in The Netherlands and Belgium. As well as supplying the well-known bicycle brand ‘Cortina’, Kruitbosch also supplies bicycle parts and accessories to store and direct-to-consumer. In order to improve their service levels, they opted for Honeywell’s Vocollect Voice solutions for their picking process.
Martin Kruitbosch, Co-owner and Parts and Accessories Manager explains; “We offer next-day delivery to all customers who order before 5pm, which leaves us minimum time to process their orders. We needed a flexible logistics solution to enable us to meet our promised service levels, which we found in Honeywell’s Vocollect voice solutions.”
The system was deployed in February 2013. Employee productivity rose immediately and their error rate has been halved.
Employee productivity increased by 30%, four processes were reduced to two
Before the introduction of Honeywell’s Vocollect solutions Kruitbosch employees had to pick, audit, pack and prepare orders for dispatch. Now the need for auditing has been eliminated due to the decrease in error rate to less than 0.05% enabled by the system, and they have been able to merge the packing and dispatch preparation into a single process – thus reducing four processes to two.
Honeywell’s Vocollect solutions also allow workers to pick up to 16 concurrent orders, representing more than a five-fold increase from the previous system where they could only pick a maximum of three at the same time. All-in-all employee productivity has increased by 30% since the introduction of voice, allowing more tasks to be completed with the same number of people.
Introducing the new system to employees
The introduction of such new systems is always a significant change for any business and can sometimes be a cause of consternation for the employees concerned. Kruitbosch took distinct measures to reassure its workforce by enabling them to play well-defined roles in the system roll-out.
Martin Kruitbosch continues, “We wanted to ensure that our employees were comfortable with the new system so we involved them at a very early stage, forming small working groups who decided, for example, which voice commands to use. As such they responded very positively to the introduction of voice”
Employee satisfaction
Esther Mijnheer, order picker at Kruitbosch states; “When we were first told we’d have to work with voice I was anxious that I wouldn’t be able to handle the computer. But now I wouldn’t go back to the old system at all. With voice I can work a lot faster – and I’m much less tired at the end of the day.”
Jan Mulder, order picker adds; “My job became a lot easier with the introduction of voice. My hands are always free, so I can pick all products more easily”
Arjen Rouw, warehouse team leader says; “When I heard we were going to use voice I was worried my work would become less interesting. But, that’s not the case at all as I still have to use my brain.”
Martin Kruitbosch concludes; “I recommend that everyone looks into using Honeywell’s Vocollect systems, I believe they will be pleasantly surprised by its advantages.”
Share it:
